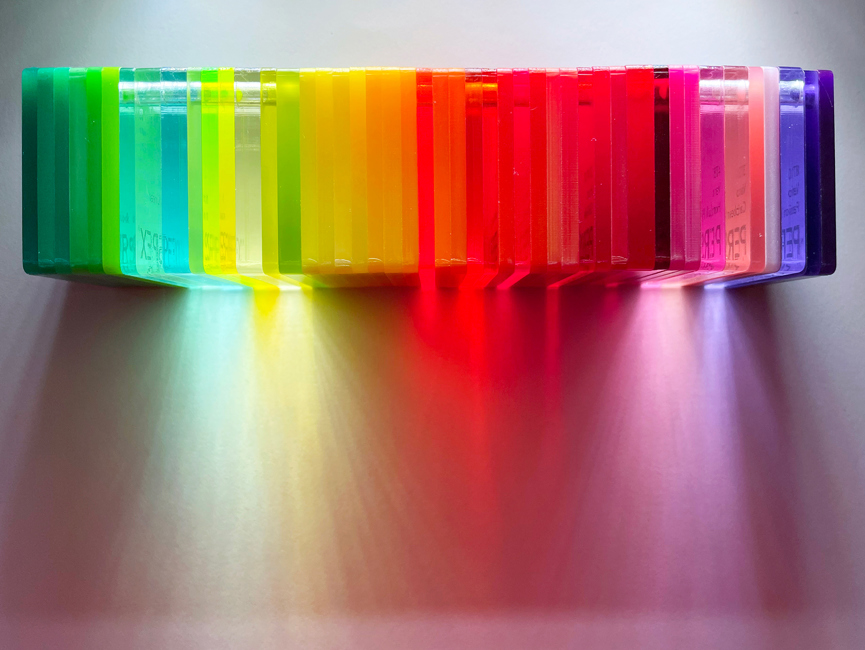
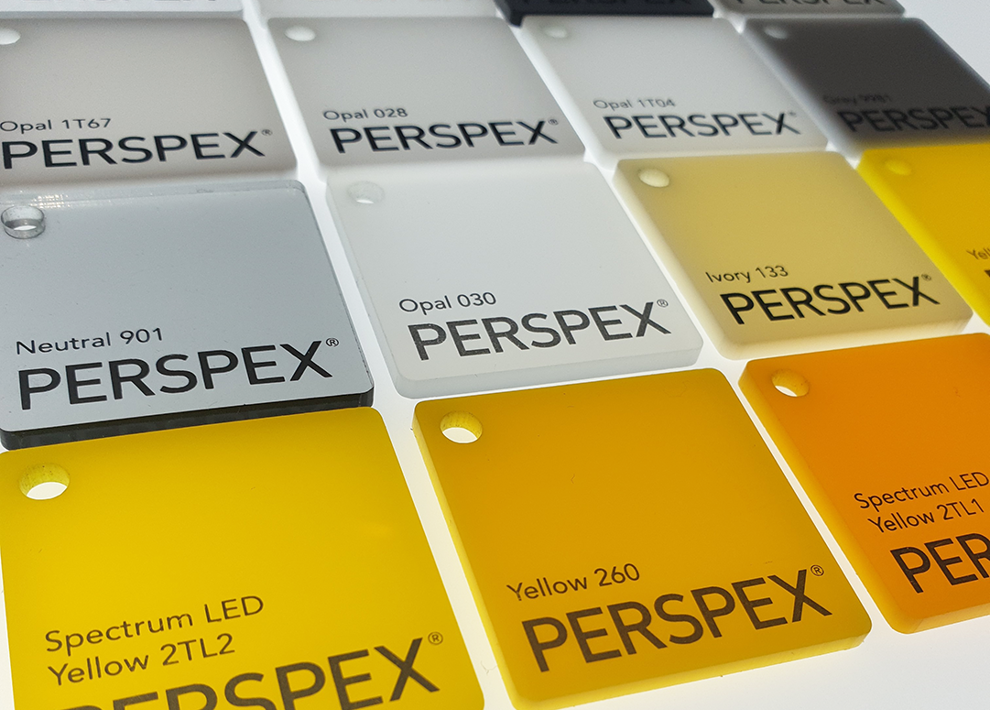
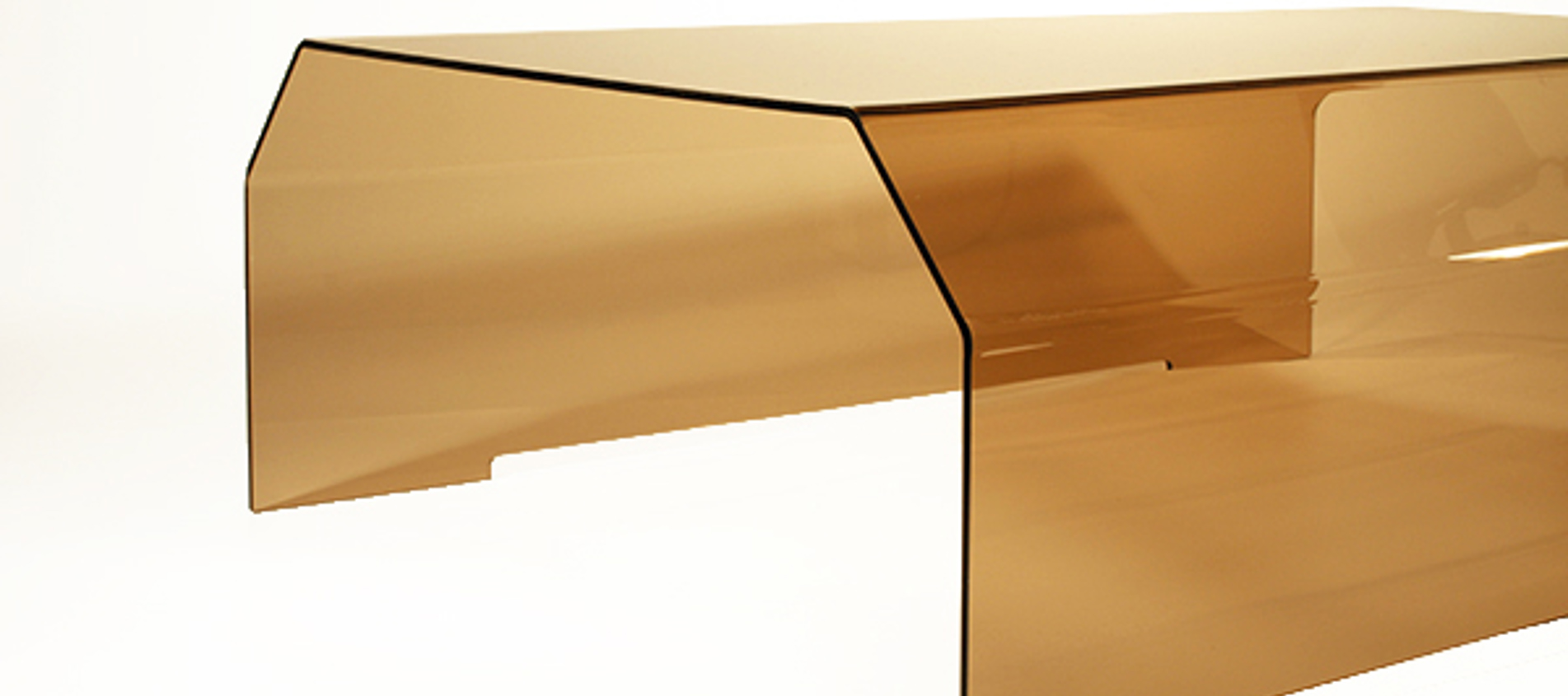

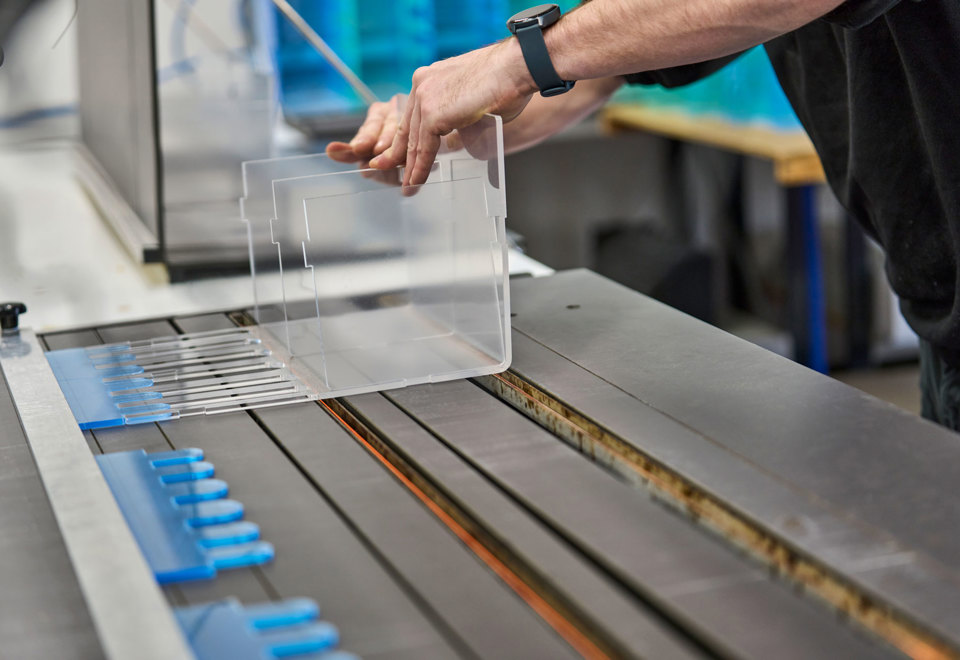
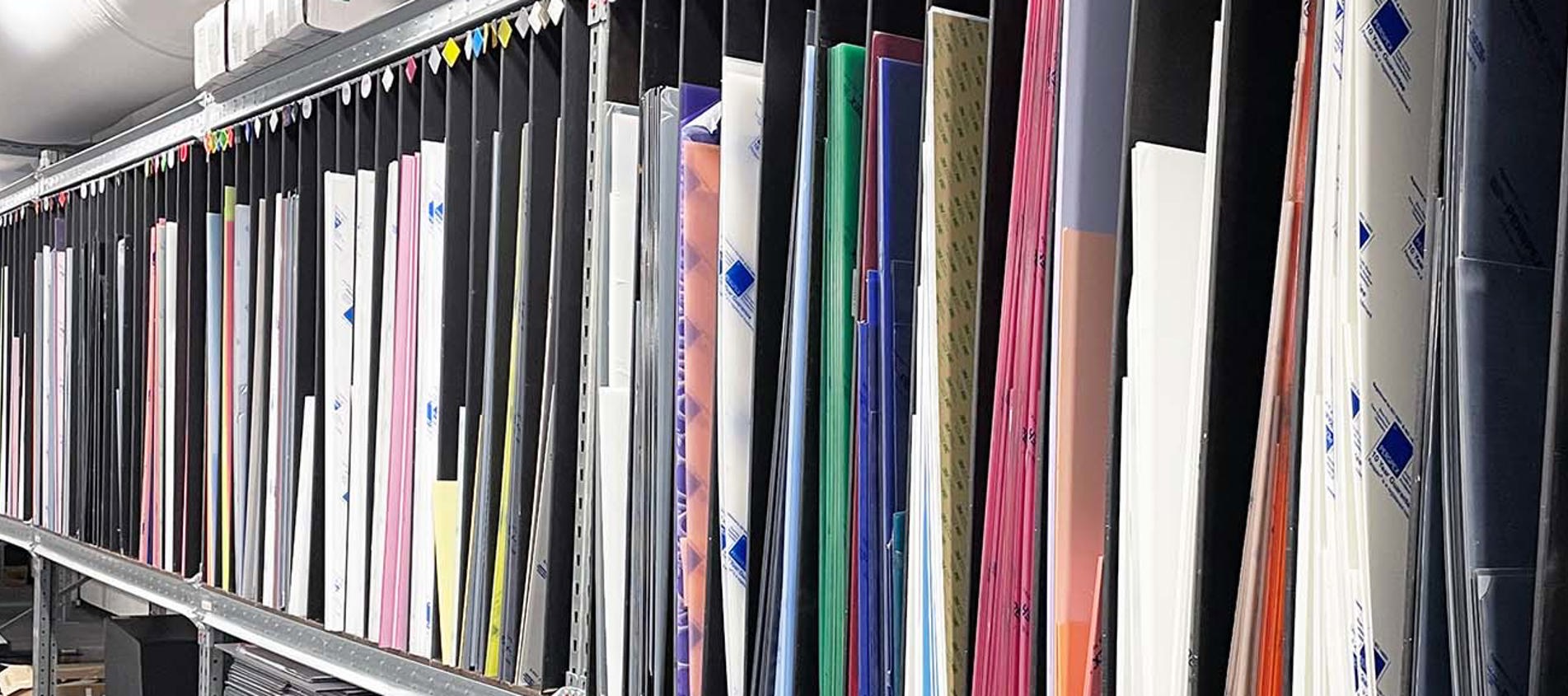
Have any questions?
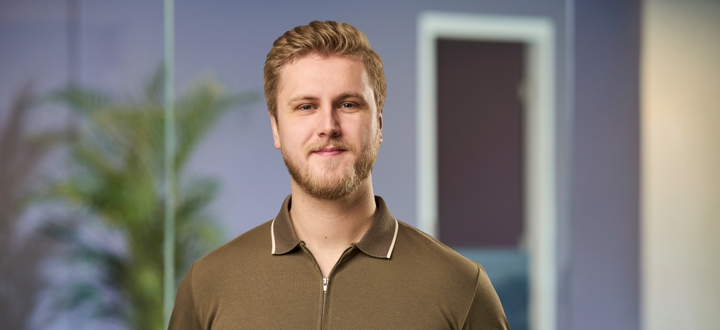
Daniel Dam Barrett
Technical Advisor & Sales
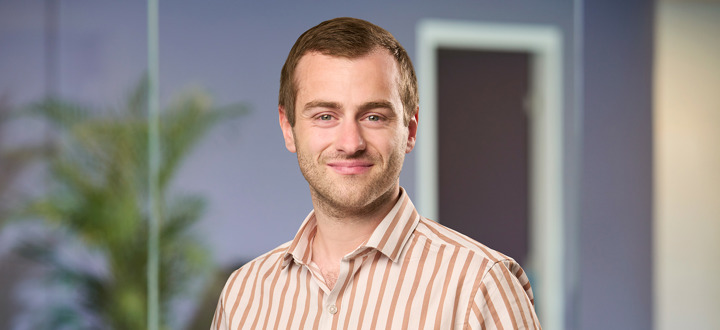
Bárður Jónsson Stórá
Sales Coordinator
Spørgsmål og svar
-
We have a large inventory of plastic materials, allowing us to accommodate requests for items made from standard materials within 8-14 business days, depending on the complexity of your components.
If your project requires more specialized plastic, such as acryl in custom colors, we typically operate within a month.
We only work with European suppliers, ensuring that we can quickly order materials tailored to your needs.
-
At Induflex, we can achieve very tight tolerances in plastic.
When you order a plastic part from us, it will comply with Danish Standard ISO 2768-1 (medium) by default. We measure the tolerances at room temperature, around 21 °C.
Of course, we can agree on different tolerances if you wish.
-
Like many other thermoplastics, acryl is stress-sensitive. Therefore, designs should be made without sharp internal corners.
If a design combines stress concentration with internal stresses, it doesn’t take much for the acryl to crack during processing, transport, or initial use.
Internal stresses are well-known in extruded acryl due to the fabrication method of the raw material, but stresses can also be created by improper flame polishing, laser cutting, or using incorrect tools.
Internal stresses in acryl can be relieved through annealing, which involves slow heating and cooling.
In clear acryl, stresses can be visually detected using two pieces of polarizing filter. Place the acryl behind a light source, lay the filters on top of each other, and observe the material through the filters while rotating them relative to each other. The stresses will now become visible.
-
Acryl is produced in two versions: cast acryl (known as acryl ST) and extruded acryl (known as acryl XT).
Cast acryl is made by mixing the components of acryl in molds. A chemical process occurs in the mold, creating a homogeneous material with the same properties in all directions.
Extruded acryl, on the other hand, is produced by continuously pressing the acryl mass through a mold while the chemical process takes place. As a result, extruded acryl is heterogeneous and has properties that vary depending on the direction, which is referred to as the extrusion direction.
Cast acryl is sometimes considered to be of the highest quality, but both cast and extruded acrylic have their advantages and disadvantages—so it is ultimately the application and desired properties of the finished product that determine which is best for your design.
Cast acryl is available in many colors, while extruded acryl is often clear (transparent), white, or black. If you order a custom color from us, it will be cast.
In terms of properties, cast acryl has higher surface durability and is therefore more scratch-resistant and more resistant to chemicals than extruded acryl.
Cast acryl sheets have a higher thickness tolerance—a cast 3 mm sheet can vary by +/- 15% in thickness, whereas extruded acryl varies by +/- 5%. The tolerance for cast acryl can therefore pose challenges for some designs, such as in relation to joints.
Additionally, cast acryl has fewer internal stresses than extruded acryl.
When processing acryl, cast and extruded acryl also behave differently.
It is more difficult to bend and shape cast acryl than extruded acryl.
When cast acryl is laser cut, there are almost no burrs, whereas extruded acryl will have burns after laser cutting.
The surface engraving of cast acryl becomes matte white, while that of extruded acryl becomes matte gray, making it less prominent in the material. Transparent acryl cannot be engraved with a YAG laser.
There are also differences in polishing between the two types. Extruded acryl can be flame polished, while cast acryl cannot.
If you are unsure whether to choose cast or extruded acryl for your design, we are happy to help you.
-
Acryl can be damaged by cleaning with alcohol, benzene, or harsh brushes that scratch the surface.
Therefore, the plastic type is best cleaned with water, regular dish soap, and a clean, soft cloth that won’t scratch the surface of the acryl. It can also be sprayed with glass cleaner (without alcohol or spirits) and wiped down with a soft cloth.
Be aware that excessive mechanical friction with a cloth or other objects against the acryl can create small scratches, which may dull the shiny surface of the material over time.
-
By sending us a STEP file or PDF with your drawings, we can quickly help determine if acryl is the right choice for your project.
We can also identify which processing method is best suited for the parts.

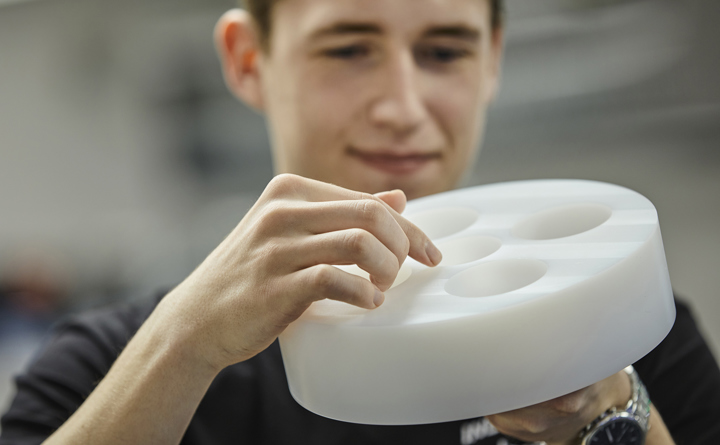
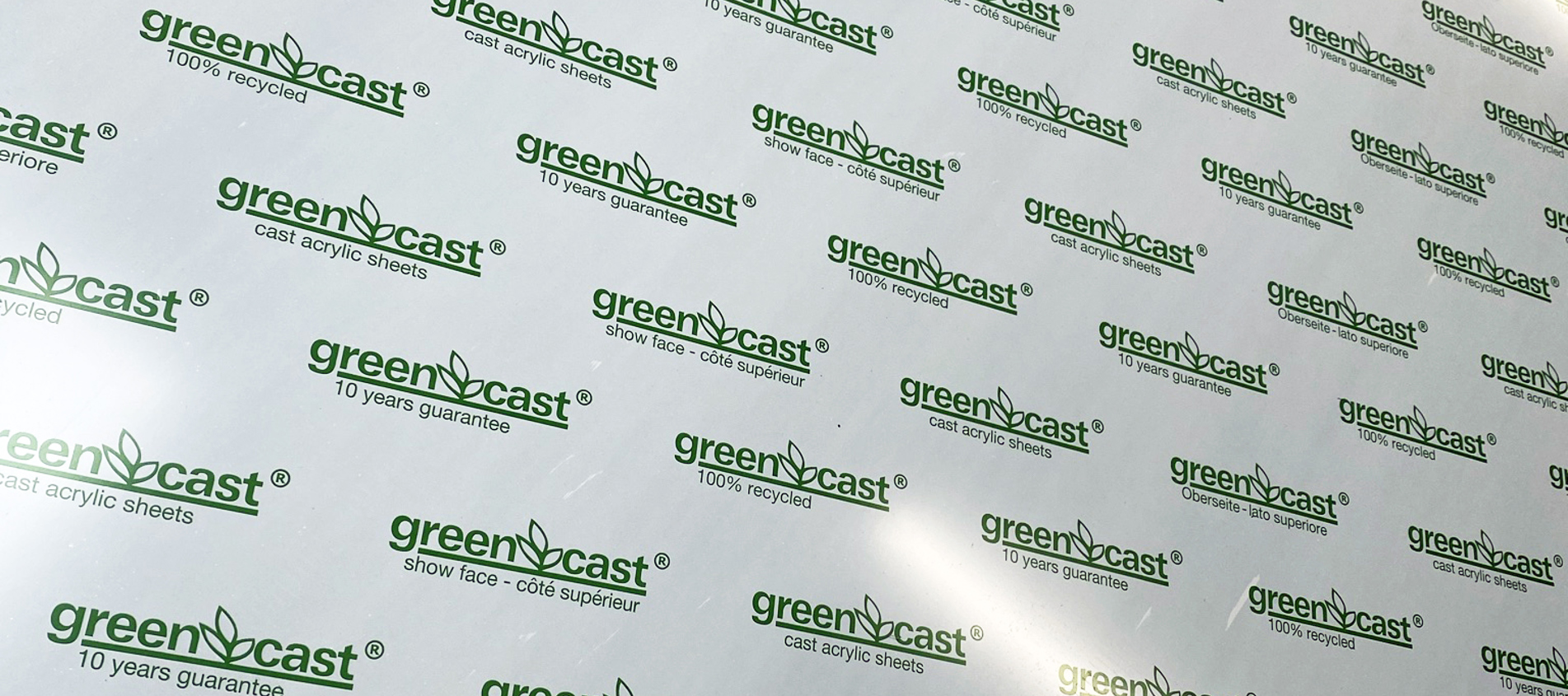
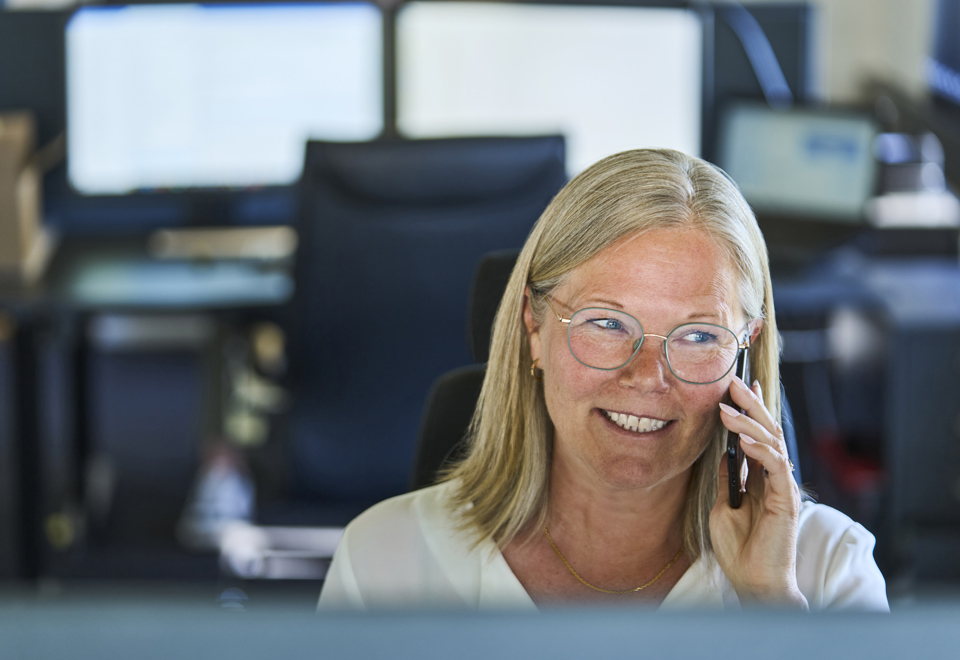